Medical-Grade vs. Industrial-Grade Silicone Tubes: What’s the Difference?
In various industries ranging from healthcare to manufacturing, silicone tubes have become indispensable due to their versatility and reliability. Understanding the distinctions between medical-grade and industrial-grade silicone tubes is crucial for ensuring optimal performance and safety in their respective applications.
Understanding Silicone Tubes
Silicone tubes are flexible, durable, and resistant to extreme temperatures and chemicals. They find usage across diverse fields such as food processing, pharmaceuticals, medical devices, automotive, and industrial processes. Choosing the correct type of silicone tube can make a significant impact on efficiency, cost-effectiveness, and compliance with industry standards.
Characteristics of Medical-Grade Silicone Tubes
Medical-grade silicone tubes are designed to meet stringent purity and biocompatibility standards. The material composition primarily includes high-purity silica-based compounds that eliminate potential contaminants. These tubes must conform to rigorous safety requirements, including being free from harmful additives that might interact negatively with biological tissues.
Sterilization and cleanliness are paramount considerations for medical-grade silicone tubes. They need to withstand multiple sterilization methods such as autoclaving, gamma radiation, and ethylene oxide without degrading. Regulatory approvals like FDA and ISO certifications further validate their suitability for medical use, ensuring they meet defined health and safety regulations.
The common applications of medical-grade silicone tubes include catheters, feeding tubes, IV drug delivery systems, wound drainage systems, and other critical medical apparatus where sterility and patient safety cannot be compromised.
Characteristics of Industrial-Grade Silicone Tubes
On the other hand, industrial-grade silicone tubes emphasize durability and resistance to harsh environmental conditions. Their material composition often incorporates reinforcing agents to enhance strength and robustness. These tubes excel in environments involving extreme temperatures, aggressive chemicals, mechanical stresses, and prolonged exposure to UV light or ozone.
The flexibility of industrial-grade silicone tubes makes them ideal for dynamic applications requiring frequent movement or bending. Quality control during manufacturing ensures these tubes maintain consistent performance under varying operational scenarios.
Typical uses of industrial-grade silicone tubes span across chemical processing, automotive fuel lines, food and beverage handling, HVAC systems, and general machinery where reliable fluid transfer is essential.
Key Differences Between Medical-Grade and Industrial-Grade Silicone Tubes
A key difference lies in the material purity and adherence to safety standards—medical-grade tubes prioritize non-reactivity and compatibility with human tissue, whereas industrial-grade tubes focus on resilience against physical and chemical deterioration.
Regulatory requirements also vary significantly. Medical-grade tubes mandate strict compliance for approval (e.g., FDA, USP Class VI) compared to relaxed but effective quality controls for industrial counterparts. Performance attributes differ based on intended application; medical-grade options offer excellent biocompatibility, while industrial versions boast superior tolerance to stress and environmental factors.
Factors to Consider When Choosing Between Medical-Grade and Industrial-Grade Silicone Tubes
The choice hinges on specific needs and scenario contexts. Analyze the intended use—whether it demands high purity for medical use or robust resistance for industrial tasks. Assess relevant regulatory constraints and compliance obligations according to industry norms.
Budget considerations often play a role too. While medical-grade tubes generally involve higher costs owing to precision and certification expenses, industrial-grade variants cater to affordability balanced with required performance levels.
Biocompatibility and ease of sterilization should remain pivotal for choices aimed at healthcare applications, given their direct interface with living tissues and necessity for absolute hygiene.
Case Studies and Real-World Applications
An enlightening example of successful implementation involves using medical-grade silicone tubing in dialysis machines, ensuring safe and efficient blood filtration for patients. Another real-world instance sees industrial-grade silicone tubes enabling seamless chemical transport within large-scale manufacturing plants, resisting corrosive substances and maintaining functional integrity over time.
Lessons derived encompass the importance of sector-specific assessments when selecting materials, factoring long-term reliability alongside immediate technical specifications.
Expert Tips for Selecting the Right Silicone Tube
Consultation with seasoned professionals or suppliers adds valuable insights tailored to niche demands. Evaluating detailed product specs and scrutinizing technical datasheets provides clarity on properties and capabilities.
Conducting preliminary trials helps verify theoretical expectations under practical conditions. Considering maintenance aspects guarantees sustained performance and extends the lifespan of selected tubing solutions.
Continual advancements in material science suggest enhancing existing formulations to yield improved safety, adaptability, and performance metrics. Growth areas in biomedical technology forecast greater dependency on specialized silicone tubing for innovative treatment methodologies. Regulatory shifts may redefine current standards, making continual adaptation vital for staying compliant and competitive.
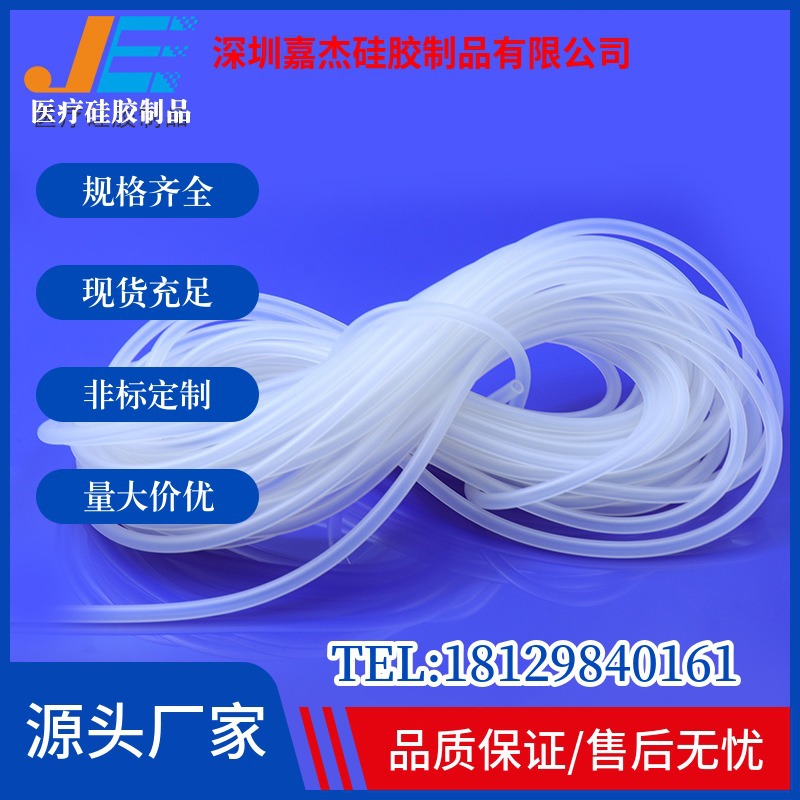